製造業では「加工精度」が製品の品質や信頼性を左右する重要な要素です。特に工作機械を扱う加工エンジニアにとって、精度の高い加工は日々の成果に直結します。この記事では、加工精度の基本的な考え方から種類、影響する要因、精度を高めるための対策までをわかりやすく解説します。
目次
1. 加工精度とは何か
加工精度とは、設計図面に示された寸法や形状に対して、実際に加工された部品がどれだけ正確に一致しているかを示す指標です。寸法、形状、表面の仕上がりなど複数の要素で構成されており、製品の性能や信頼性に大きく関わります。
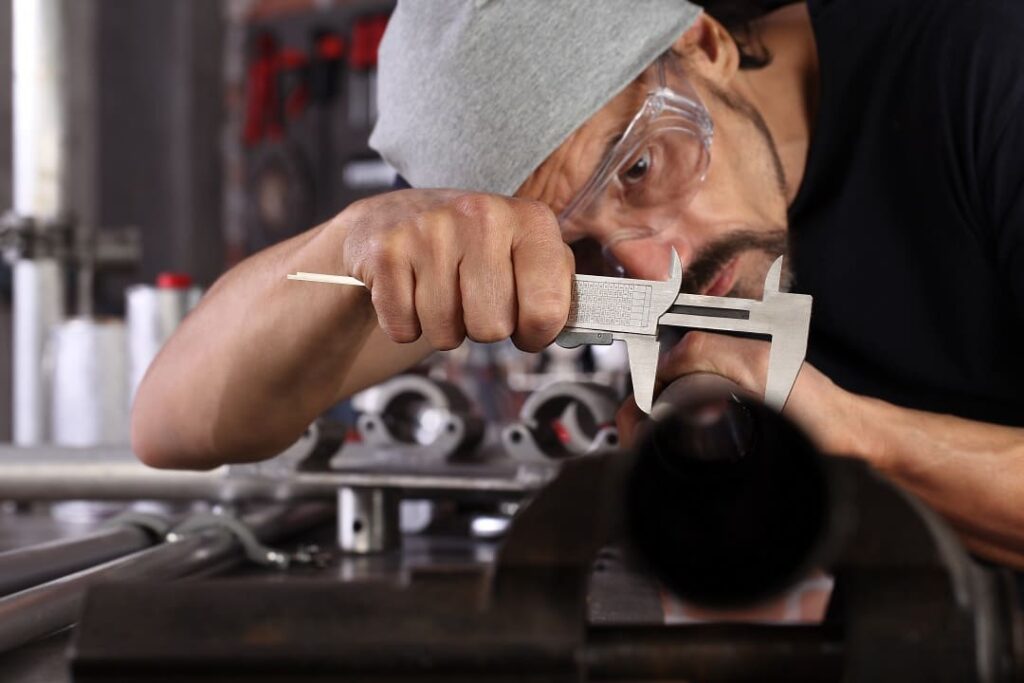
加工精度の定義
日本機械学会では、加工精度を以下のように定義しています
工作精度ともいい,加工後の工作物の品質レベルを示す尺度で,寸法精度,幾何学的形状精度,表面粗さなどがある.
引用元:https://www.jsme.or.jp/jsme-medwiki/doku.php?id=18:1002041
これらの精度は、製品が設計通りに機能するための土台であり、生産効率や不良率にも大きく影響します。
JIS(日本産業規格)における加工精度
加工精度の評価は、JIS(日本産業規格)によって体系的に定められています。これにより、現場では統一された基準で精度を管理でき、品質の安定や工程間の整合性が保たれます。JISは、精密加工における信頼性を支える重要な基準です。
加工精度を測定する方法
加工精度の測定には、目的や求められる精度に応じてさまざまな方法があります。寸法の確認にはノギスやマイクロメータが使われ、より複雑な製品の評価には三次元測定機や形状測定機が活用されます。形状や表面の仕上がりには専用の測定器が使われ、これらの結果を工程に反映することで、精度の向上や不良の削減につながります。
加工精度と公差の関係
加工精度と公差は密接に関係しています。公差は、設計上許容される寸法の誤差範囲のことであり、加工精度とは、その範囲内に寸法を正確に収める能力を指します。図面に示された公差に対して加工精度が高ければ、製品の信頼性が向上し、部品が他の部品と正確に組み合うようになります。これにより、組立作業の安定性や部品の交換のしやすさにもつながります。
加工精度の限界とは
加工精度には、機械や工具、測定機器、作業環境などの影響によって、どうしても超えられない限界があります。たとえば、ナノメートル単位の精度を目指す場合、機械のわずかな振動や熱による変形を完全に防ぐのは非常に難しいです。また、使う測定機器にも誤差があるため、理論通りの寸法を正確に確認することにも限界があります。
こうした制約を理解することで、過剰な精度を求めすぎてコストや作業負担が増えるのを防ぎ、現実的で効率的な品質管理が可能になります。
2. 加工精度の種類
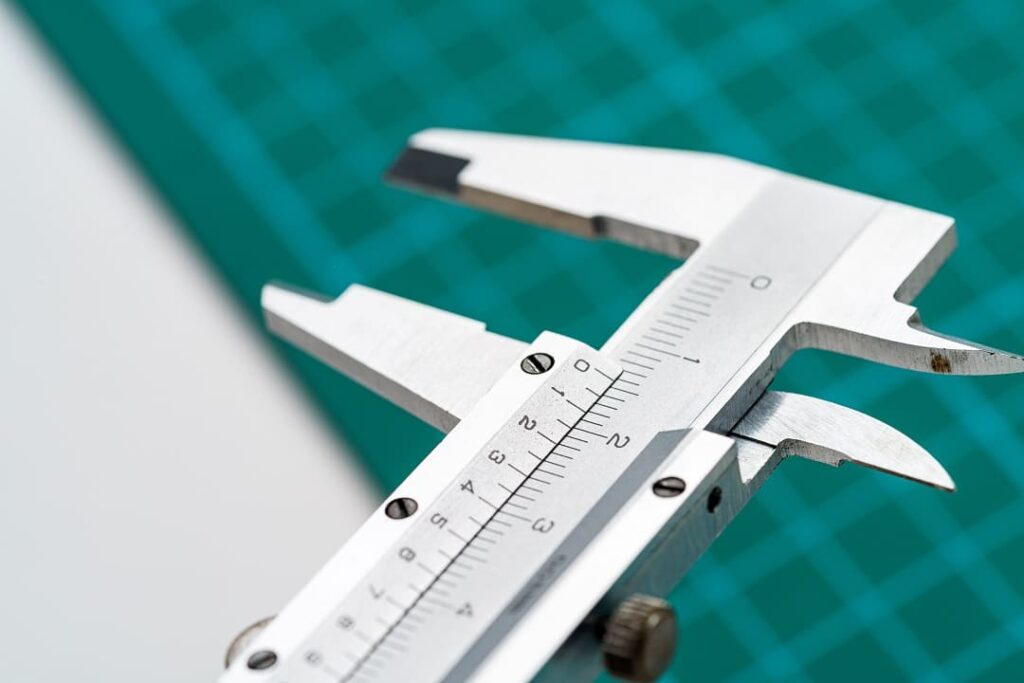
加工精度は一つの指標ではなく、複数の観点から評価されます。代表的なものに「寸法精度」「形状精度」「表面粗さ」「角度精度」などがあり、それぞれに応じた測定方法と管理すべきポイントがあります。
寸法精度
寸法精度は、部品の長さや直径などの寸法が設計値にどれだけ近いかを示します。JIS規格に基づく公差等級が設定されており、精密部品ではミクロン単位の管理が求められます。寸法精度は最も基本的な加工精度の指標です。
形状精度
形状精度は、加工された部品の幾何学的な形状が理想形状からどれだけずれているかを評価します。真円度、平面度、円筒度などが代表的な項目で、回転体や摺動部品などでは特に重要です。高精度な形状は製品の性能に直結します。
表面粗さ
表面粗さは、加工面の滑らかさを数値で表したものです。中心線平均粗さ(Ra)などの指標が用いられ、摩擦や耐久性に影響します。高精度な表面仕上げは、摺動部や密着部での性能向上に寄与します。
角度精度
角度精度は、部品の傾きや角度が設計通りに加工されているかを示します。特に組み立て精度が求められる部品では、角度の誤差が全体の精度に大きく影響します。角度測定には専用の治具や測定器が用いられます。
3. 加工精度に影響を与える10の要因
加工精度は機械の性能だけでなく、工具の状態、加工条件、環境、素材の特性、切削液など、さまざまな要因によって左右されます。これらを理解し、適切に管理することが高精度加工の鍵です。
①工作機械の性能
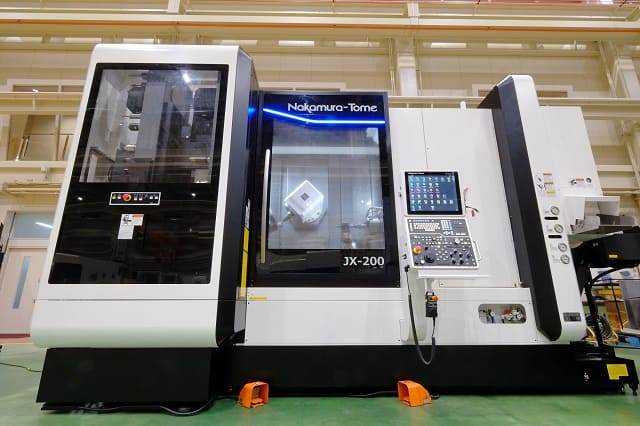
加工精度を左右する基本的な要因のひとつが、工作機械の性能です。なかでも機械構造の剛性は非常に重要で、剛性が不足していると、加工中に工具やワークが微小に振動したり、切削抵抗によって機械部品がたわんだりして、寸法や形状に誤差が生じやすくなります。たとえば、薄肉部や長尺ワークを加工する際には、わずかなたわみが加工精度に大きく影響します。
また、送り軸の位置決め精度や繰り返し精度、主軸の回転精度も精度確保の鍵となります。これらが高精度であるほど、加工中の位置ズレや振れが抑えられ、狙った寸法や幾何形状により近づけることができます。
また、長期間の使用によって、ボールねじやリニアガイドの摩耗、主軸ベアリングの劣化が進むと、加工精度は徐々に低下します。これを防ぐには、幾何精度のチェックや主軸の振れ測定、潤滑状態の確認など、定期的な保守管理が重要です。
②工具の状態
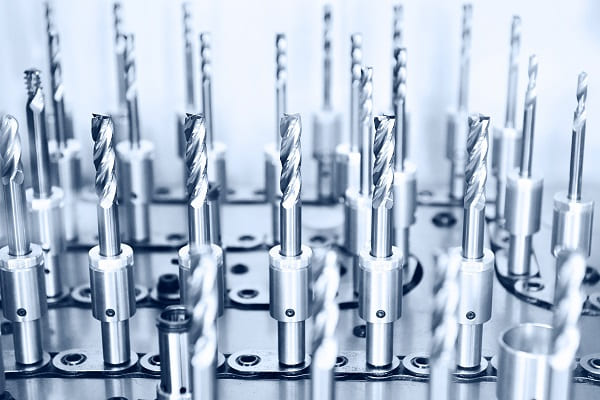
工具の状態は、加工精度に直接影響します。摩耗が進むと寸法が設計値から外れたり、加工面にバリが出たりすることがあります。特に仕上げ加工では、摩耗によって表面の滑らかさが損なわれ、製品の性能や見た目に影響します。工具の寿命を把握し、適切なタイミングで交換することが重要です。
使用履歴の記録や摩耗状態の定期チェックなど、工具管理を徹底することで、安定した加工精度が保てます。
③切削条件
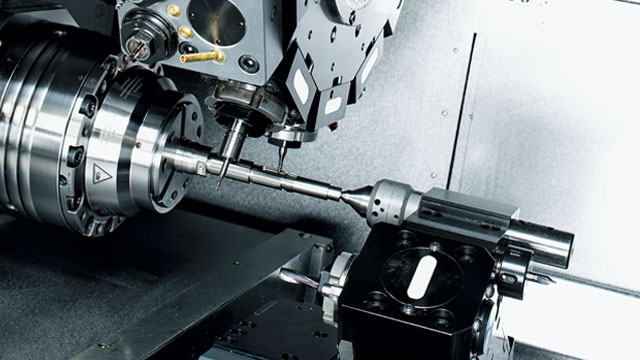
切削条件の設定は、加工精度に大きく関わります。切削速度、送り速度、切込み量が適切でないと、加工中に熱が発生し、素材が膨張・変形して寸法誤差が生じます。特に高精度加工では、熱変形を抑えるための条件設定が重要です。
素材や工具の特性に合わせて最適な切削条件を選ぶことで、加工面の品質や寸法の安定性が向上します。
④加工時の環境
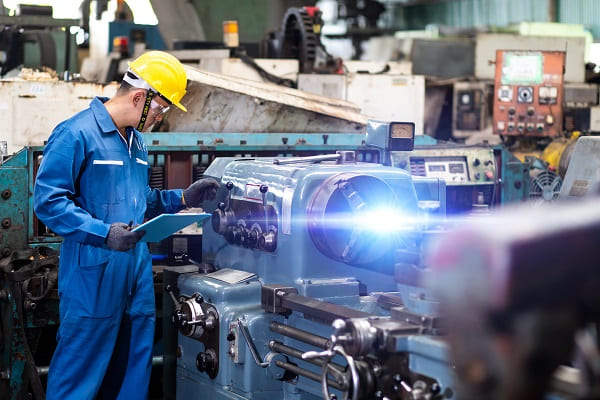
加工精度は、作業環境の影響も大きく受けます。たとえば温度が変化すると、機械や素材がわずかに伸び縮みし、寸法に誤差が出ることがあります。特に精密加工では、室温を一定に保つことが重要です。振動も加工中のブレや位置ずれの原因となり、仕上がりに影響します。さらに湿度が高いと、素材が膨張したり錆が発生したりして、長期的な精度に悪影響を及ぼします。
そのため、高精度な加工には、空調による温湿度管理や振動対策など、作業環境の整備が欠かせません。
⑤素材の性質
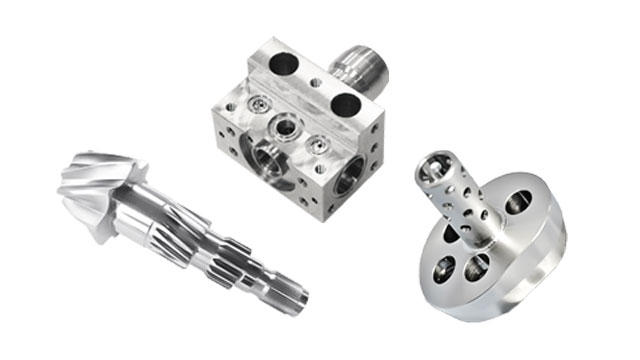
加工する素材の性質も、精度に大きく影響します。硬い素材は工具の摩耗が早く進み、加工面に不具合が出やすくなります。一方、柔らかい素材は加工中に変形しやすく、寸法精度の確保が難しくなります。また、熱伝導率が低い素材は加工熱がこもりやすく、熱膨張による寸法誤差が発生しやすくなります。素材の特性を理解し、それに合った工具や加工条件を選ぶことが重要です。
⑥切削液の種類
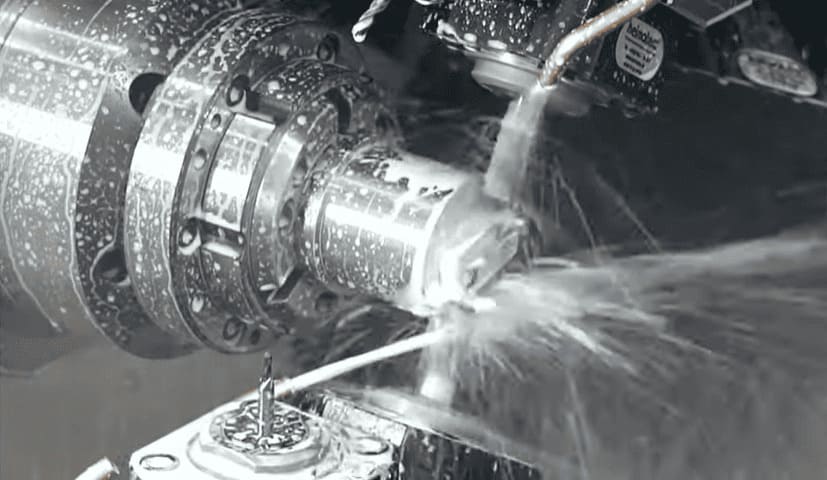
切削液は、加工中の冷却・潤滑・洗浄の役割を果たし、加工精度の安定に貢献します。冷却効果で加工熱を抑え、寸法変化や工具摩耗を防ぎます。潤滑効果は摩擦を軽減し、滑らかな加工面を実現します。洗浄効果は切りくずを除去し、加工面の傷や不具合を防ぎます。
切削液には水溶性、油性、高性能タイプなどの種類があり、加工内容や素材に応じて適切に選定する必要があります。なお、高性能タイプの中でもシンセティック系(合成油ベース)の切削液については、塩素系添加剤などを含む場合があり、機械や環境への影響を考慮して中村留では使用を禁止しています。
⑦治具・チャック
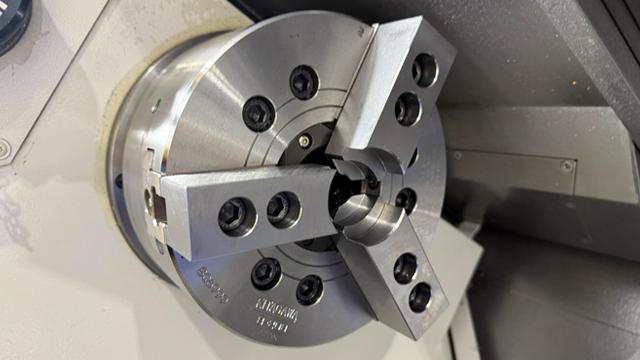
治具やチャックは、加工物を正確に固定するための装置であり、加工精度に直結します。固定が不十分だと、加工中にワークが動いて寸法や形状に誤差が生じます。一方で、クランプ力が過剰な場合は、ワークが変形してしまい、やはり精度に悪影響を及ぼします。特に薄肉や柔らかい材質のワークでは注意が必要です。
高精度加工を実現するには、繰り返し位置決め精度やクランプ力の安定性に加え、ワークの形状や材質に応じた最適な治具設計とチャックの選定が不可欠です。
⑧加工順序と工程設計
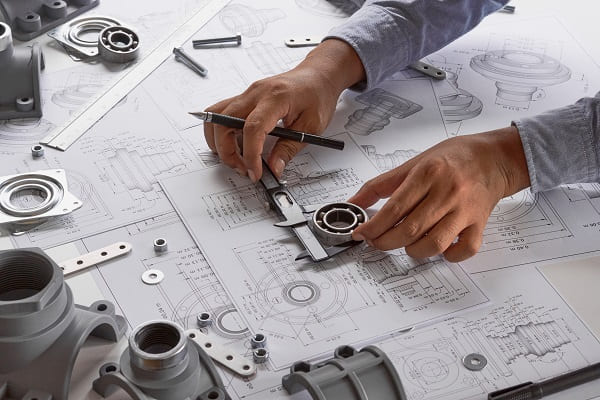
加工順序や工程設計は、加工精度の安定に大きく関わります。荒加工で大まかな形状を整えた後に仕上げ加工を行うことで、工具負荷や熱変形を抑え、寸法精度を確保しやすくなります。熱の影響を受けやすい工程を後に回すなど、順序の工夫によって誤差を最小限に抑えることが可能です。
多工程加工では、工程が変わるごとにわずかな位置ずれや精度のずれが生じることがあります。そのため、各工程後にワークの位置ずれを確認し、必要に応じて測定や再調整を行うことが、安定した加工精度の維持に不可欠です。
⑨測定機器の精度
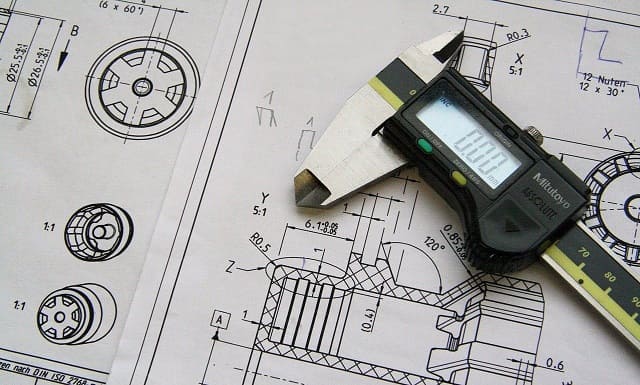
加工精度を正しく評価するには、使用する測定機器の精度が高く、信頼性のあるものである必要があります。三次元測定機(CMM)や形状測定機などは、微細な寸法や形状の違いを正確に捉えることができ、高精度な加工の評価に適しています。
ただし、これらの機器も定期的な校正や使用環境の管理が必要です。測定誤差が加工精度の判断を誤らせることがあるため、機器の選定と運用には十分な注意が必要です。
⑩オペレーターの技能
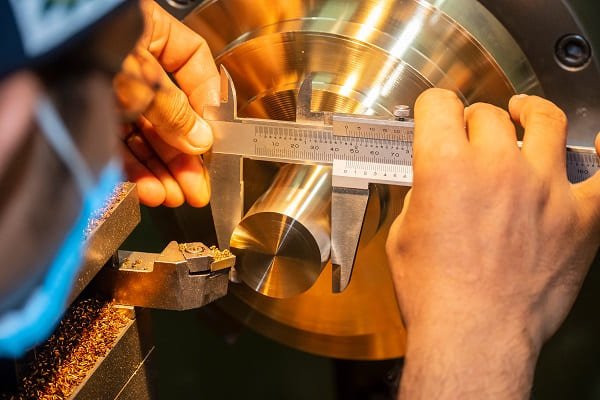
加工精度は、設備や工具だけでなく、オペレーターの技能にも大きく左右されます。工具の取り扱いや加工条件の設定、異常の早期発見など、経験に基づく判断力が精度維持に貢献します。熟練したオペレーターは微細な変化にも気づき、適切な対応が可能です。
教育や技能の継承を通じて現場全体の技術力を高めることが、安定した加工精度の確保につながります。
4. 加工精度を向上させるための対策
加工精度を高めるには、機械性能だけでなく、現場での管理や技術的な工夫が不可欠です。温度管理、工具管理、測定技術の活用、IoTやAIなどのデジタル技術の導入が効果的です。
各種管理の徹底
加工精度を安定させるには、温度管理や機械の定期点検、工具の摩耗管理など、日常的な管理業務の徹底が重要です。特に高精度加工ではわずかな変化が製品品質に影響するため、管理の精度が問われます。
加工プロセスの見直し
加工工程の設計を見直すことで、精度のばらつきを抑えることができます。例えば、荒加工と仕上げ加工を分ける、熱変形を考慮した順序にするなどの工夫が有効です。多工程加工では、各工程の精度管理が特に重要です。
測定とフィードバックの活用
三次元測定機や形状測定機を活用することで、加工後の寸法や形状の精度を高精度に評価できます。測定結果を工程にフィードバックすることで、次回の加工条件を最適化し、継続的な精度向上につなげることが可能です。
IoT・デジタル技術の活用
IoT技術を活用すれば、加工中のデータをリアルタイムで取得・分析でき、異常の早期発見や条件の自動最適化が可能になります。AIによる加工条件の提案や、クラウド連携による品質管理の効率化も進んでいます。
5.加工精度に関する最新トレンド
ナノレベルの加工やAIによる条件最適化など、加工技術は急速に進化しています。環境負荷を抑えながら高精度を実現する技術も注目されており、今後の製造業において重要なテーマです。
中村留精密工業も、複合加工機やソフトウェアなどの開発を通じて、加工精度向上に向けた技術革新を積極的に進めています。
まとめ
加工精度は、製品の品質と信頼性を支える重要な要素です。今後はデジタル技術の進化により、より高度な精度管理が求められるようになるでしょう。加工エンジニアには、技術力だけでなく、管理力や改善力も求められる時代です。
日々の業務では、工具の状態確認、加工条件の見直し、測定結果の分析といった地道な取り組みが、精度向上に直結します。チーム内での情報共有や継続的な改善活動を通じて、現場全体の精度レベルを高めることが可能です。